Sawston Unity Campus
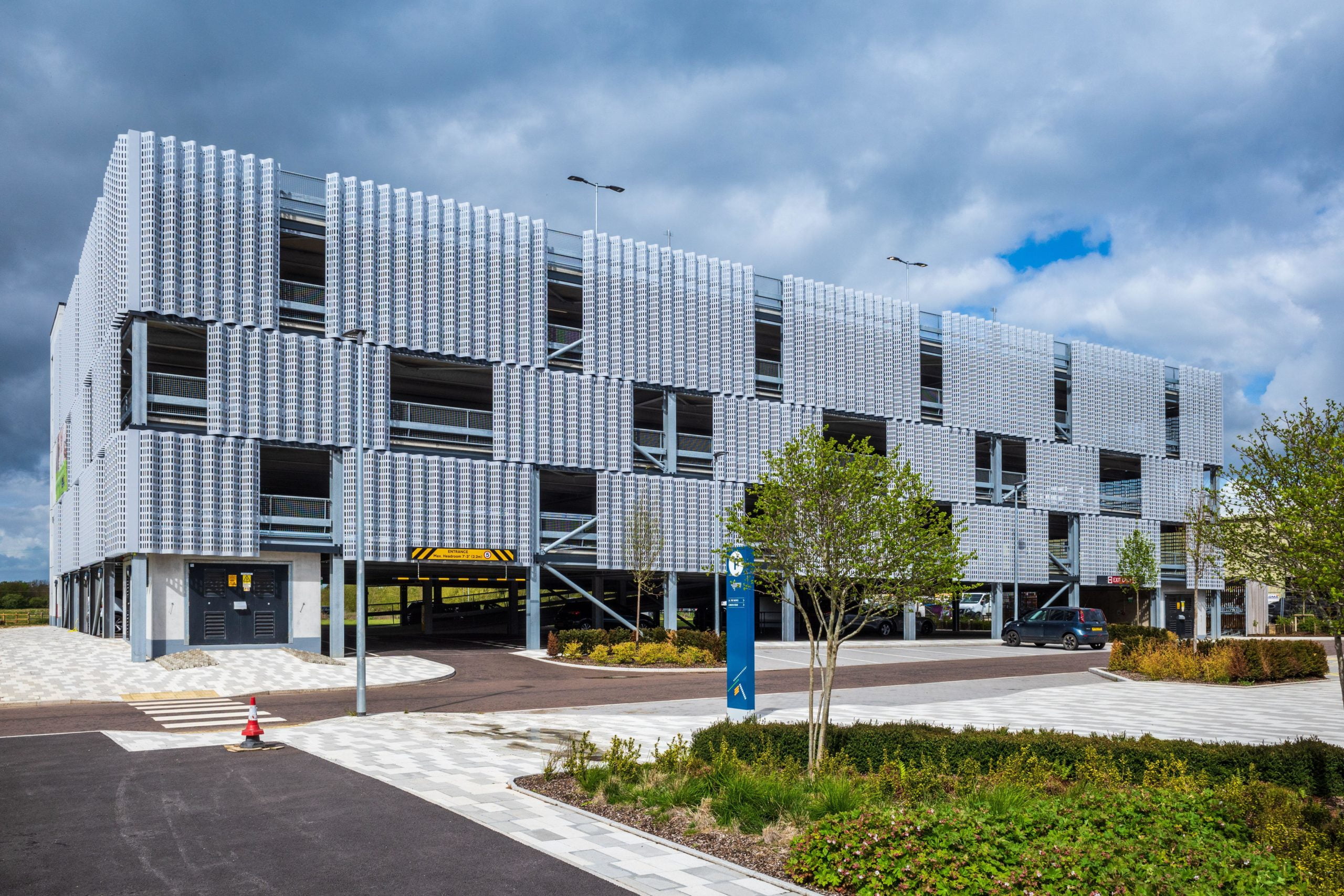
Sawston Unity Campus multi-storey car park, clad in 2,600m2 of Locker laser-cut aluminium sheets, complete with graduated radiused vertical corrugations.
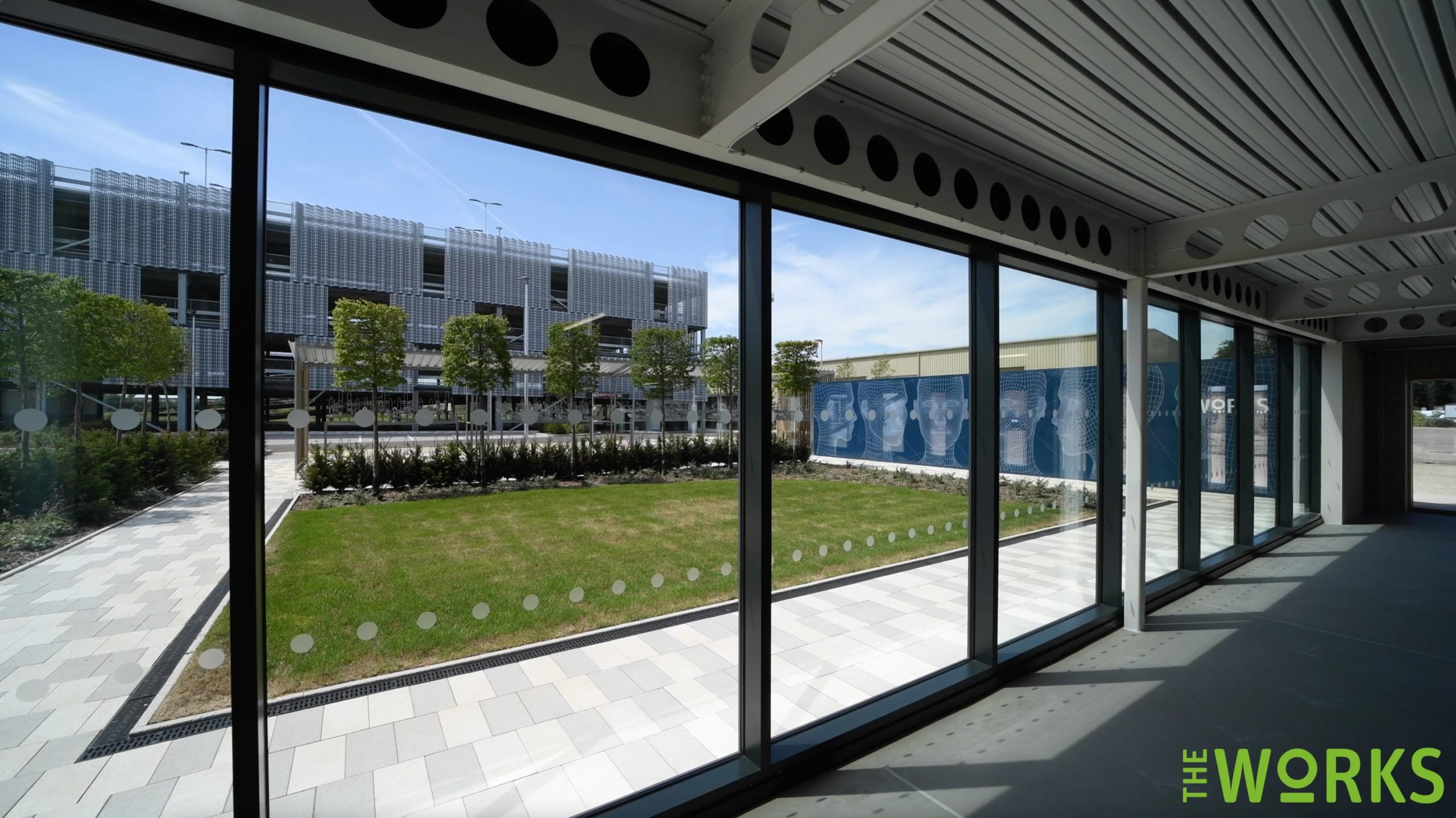
Photo kindly supplied by Unity Campus, with help from Limewash.
Locker successfully completed the full design, engineering, fabrication and installation of this project on time and within budget for Bourne Group.
The Architectural practice was Nicholas Hare.
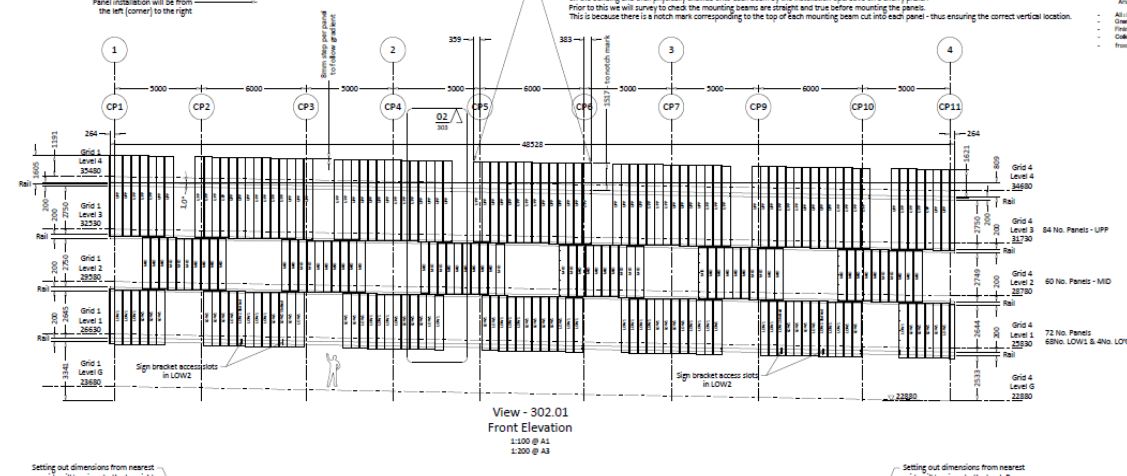
Design challenges
- Each panel had identical sinusoidal corrugations. The perforated pattern, as well as the depth and wavelength of the profile, can be varied to create a bespoke facade.
- The panels were only 2mm thick but had to vertically span up to 3m unsupported. The radius profile of the panels had to be deep enough to impose the required rigidity.
- The constraints of the rolling tool had to be considered when determining radii.
- The panels were designed to overlap enabling neighbouring panels to share common fixings.
- Wind, snow and ice forces were considered.
- The design maintains rigidity whilst having a 40% laser-cut open area for air flow.
- The slot centres were adjusted to take account of the sinusoidal radii.
- The drawing extract below shows a typical laser-cut sheet prior to, and following radius forming:
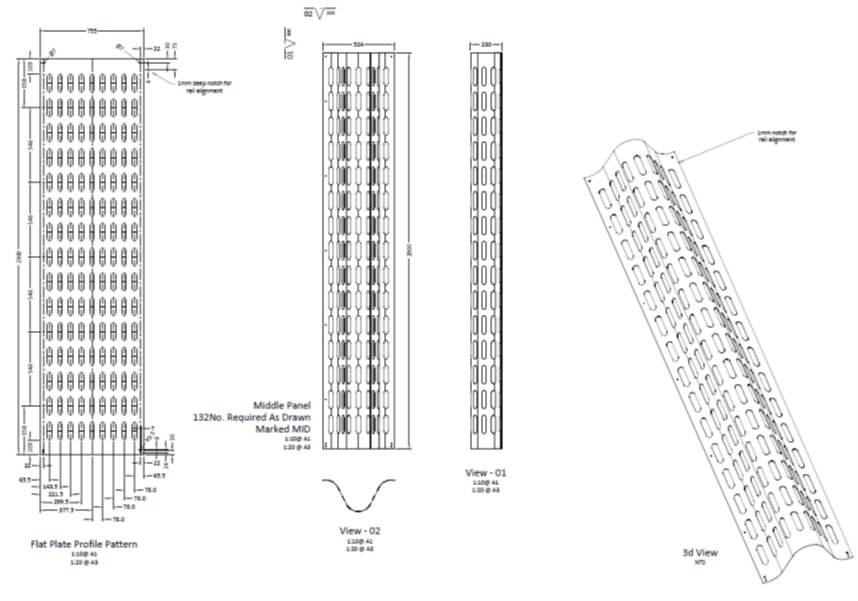
Fabrication Challenges
- Perforation slots had to be laser cut prior to forming the radii.
- The slots were not to distort during the radius forming.
- The perforated sheets had to be incrementally “bumped” in a break press to form the exact radii.
- The sinusoidal radii had to be consistent from panel to panel.
- The panels were grit blasted prior to being polyester powder-coated. The grit blasting process removes the toolmarks.
- The corner panels were site measured and installed last.
- The laser cut panels had to be consistently accurate to the millimetre as they could not be altered on site.
- The following images show the mesh panels laser-cut in their unformed state and in their radiused condition: -
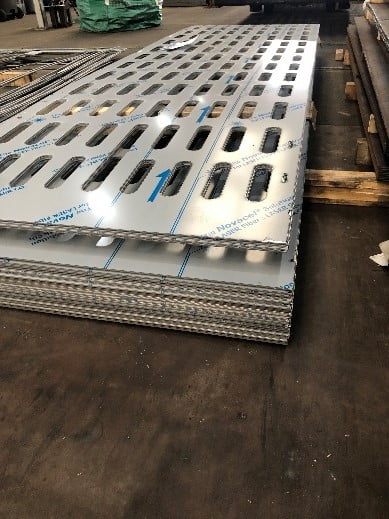
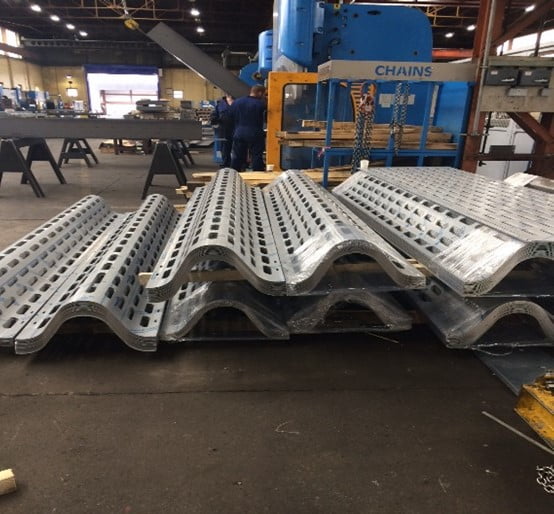
Installation Challenges
- Setting out of the panels was key to the project success to avoid accumulative error. Our site careful survey avoided abortive works where steelwork was out of alignment.
- The extract below shows how we had to adapt our setting out to accommodate the slope in the building from left to right. This we had to stagger each panel location by 8mm.
- Installation was undertaken from all-terrain scissor lifts. No lifting gear was needed.